High-Performance DC-Link - Overview
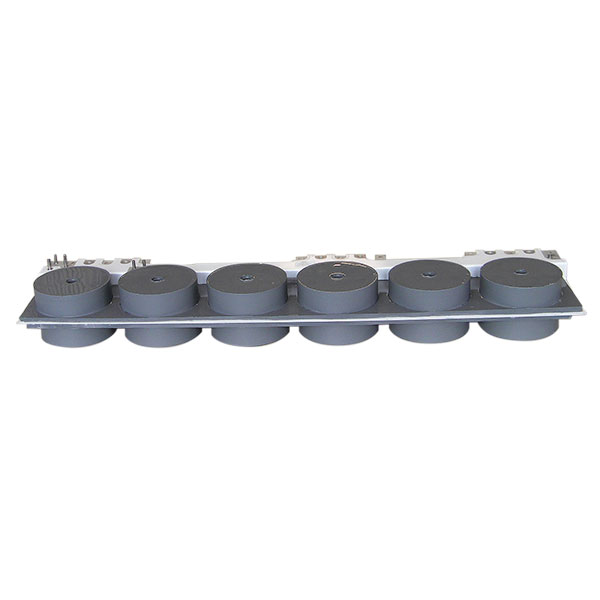
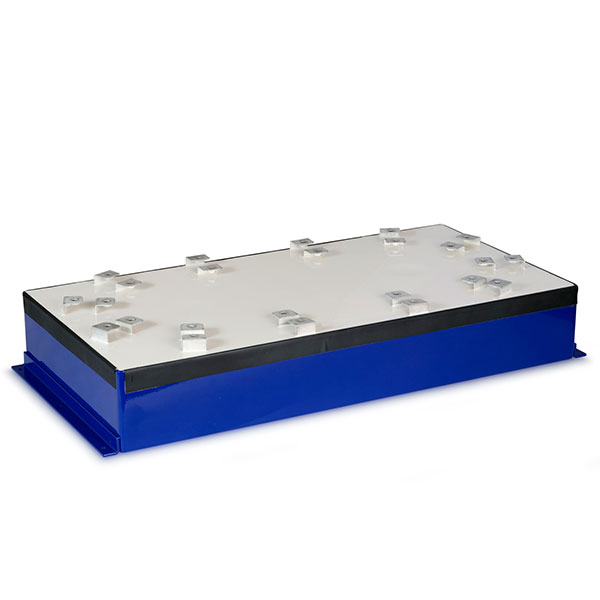
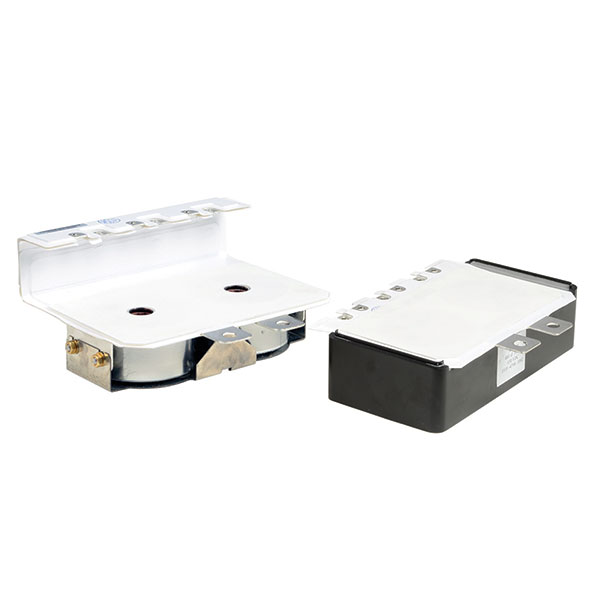
The DC link is a critical component for high-power inverters utilizing fast switching that is often overlooked during the initial stages of design. The DC-link capacitor draws a continuous low-frequency current from the DC source while supplying the charge needed for the fast switching events and effectively functions as a charge pump. Traditionally, the DC link capacitor has been treated as an afterthought of the design with a crude bus structure implemented to connect with conventional commodity capacitor elements. However, efficient fast switching using advanced silicon and wide bandgap devices requires a carefully designed DC link bus topology with tightly integrated capacitors. The Advanced Conversion annular form factor film capacitor is ideally suited for “surface mounting” to an optimized bus structure that interfaces with the switch modules. This patented approach combined with bus cooling provides a very high Ampere per mico-Farad rating to allow the smallest possible capacitance while simultaneously minimizing the commutation loop inductance. As such, the micro-Farads per kilo-Watt is defined by inverter control limitations rather than by capacitor life and the DC bus can be safely operated at a higher voltage due to reduced overshoot during turn-off. Equivalent series inductance values of less than 5nH are readily achieved using the right switch module with an appropriate connection design.
Please download our DC Link Technology Overview presentation (pdf link) for more information.
Optimized Bus Structures
Advanced Conversion specializes in complete DC-link solutions including the design and fabrication of the bus structure. We made the decision to bring this capability in house to provide faster lead times along with advanced design and fabrication capabilities for custom designs. Our unique patented and proprietary technology for mounting annular form factor windings to terminals and bus layers eliminates thermal expansion mismatch problems and eliminates the weight and cost of redundant copper that occurs when conventional discrete capacitors are mounted on a bus. The surface mounting approach also eliminates through-hole connections, maintaining high current capability, and preserves the surface of the bus opposite the capacitor for other components or direct interfacing with a cooling block. We support a variety of electric vehicles, aerospace, alternative energy, and grid-tied applications with this novel technology. Note that Advanced Conversion also offers a suite of optimized discrete capacitors and high-performance standard capacitor/bus “test kits” designed around popular switch module packages.
Working with our customers
Advanced Conversion best serves our customers by engaging early in the design process, working to understand the application, and mutually agreeing upon a practical specification. The capacitor winding can be considered analogous to the die in a solid-state device as the basic functional element which must then be properly packaged and interconnected. One or more windings are specified to meet the capacitance need subject volumetric requirements and the mission profile of the DC link voltage and ripple current, exactly the same as paralleled die are specified in a switch module. However, the capacitor element(s) must be fully integrated with proper electrical and thermal coupling to the customer system to achieve the best solution. Ultimately, the capacitor/bus structure of the DC link defines the backbone of the inverter topology and has a significant impact on both the commutation inductance and thermal performance. Lastly, the capacitance solution is the single largest influencer on volume for the end system.
Advanced Conversion provides a high level of application engineering support for our customers using the following process:
- Provide a shopping list of DC-link parameters for the customer to fill out (pdf)
- Sanity check of capacitor size given complete mission profile
- Budgetary quotation for design and custom prototype build
- 50% down payment required to commit engineering resources for custom projects
- Detailed review and finalization of the customer specification
- Thermal and electrical analysis if required
- Demonstrate required life given mission profile
- Work full mechanical design details with customer and submit final CAD for approval
- Final quotation for prototype build
- Prototype build
Our team, once committed, can usually work as fast or faster than the customer can interact with the design dialog. Typical design projects take from 4 – 16 weeks but that is usually customer-driven.
Prototypes can be built in 8 – 10 weeks for many designs. This is faster than just the bus bars themselves from typical industry sources.
We welcome your application challenges. Please contact us at this email to get the process started.
Test kits
A properly designed DC link is essential to properly evaluate switch module performance. Advanced Conversion offers a family of standard capacitor/bus test kits to support next-generation modules from vendors including the Infineon HYBRIDPACK DriveTM. These kits were actually developed at the request of the semiconductor vendor to enable customers to benchmark advanced semiconductor packages with the lowest possible inductance connections and RMS current capability. Some of these industry-leading outcomes are promoted in application notes and performance figures published by the vendors.
We offer a number of cap/bus test kits as standard products which are kept in stock to allow our customer to evaluate our technology with high-performance switch modules. In many cases, customers will evaluate a standard kit and then customize it to their exact requirements once the required performance has been demonstrated. We are continuing to develop new test kits upon request.
Visit our Products page for more details.
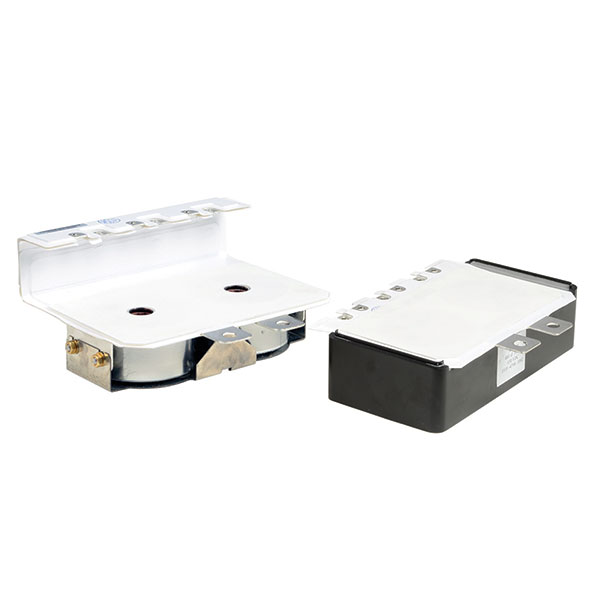
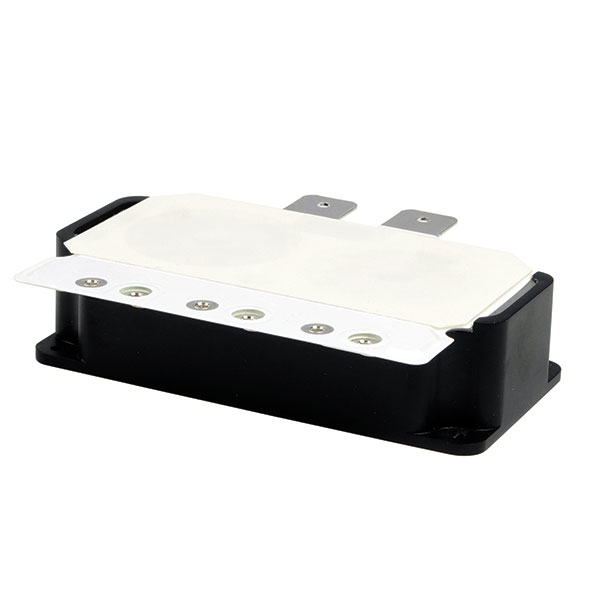
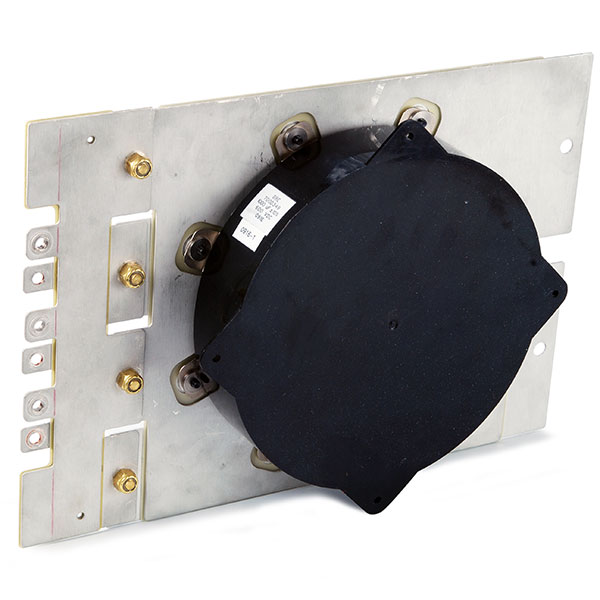
Bus fabrication capabilities
Advanced Conversion has the design expertise, vendor supply base, and internal capabilities to provide optimized bus solutions with faster lead time than the traditional bus vendors. We offer bus structures integrated with our unique surface mounted annular form factor film capacitors and also provide bus bars alone for key customers. In addition, Advanced Conversion provides high voltage AC and DC test capabilities and partial discharge measurement equipment.
Materials
- Bus conductors
- Aluminum
- Copper
- Various plating options
- Insulation
- Powder coat
- PET sheets
Construction
- Stacked
- Ideal for flat structures
- No edge seal
- Shortest lead time – 4 weeks
- Least expensive
- Minimal tooling expense
- Laminated
- Rolled or extended edge seal
- Better feature density than stacked
- More complicated tooling
- Tighter tolerances than stacked design
- Best Inductance possible
- 6 – 8 week lead time typically
- Powder-coated
- Most footprint efficient
- Best feature density capability
- Good inductance performance – better than stacked design
- Tighter tolerances than stacked design
- 4 – 6 week lead time typically
We work closely with our customers to define the best bus approach for their specific application to balance cost, lead time, and performance requirements.
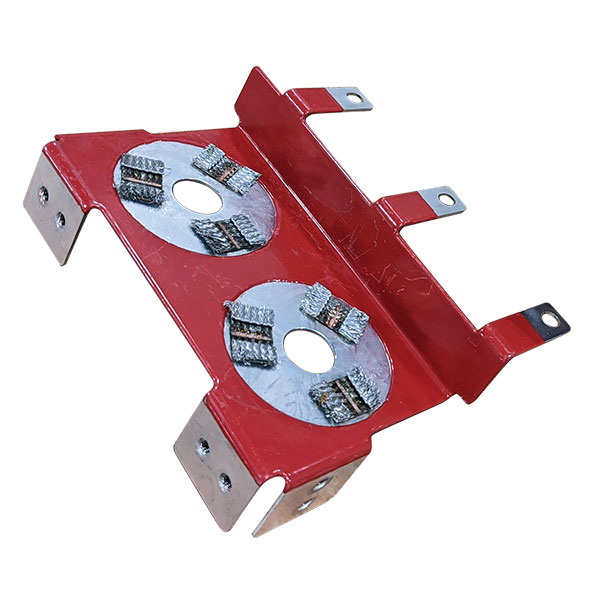

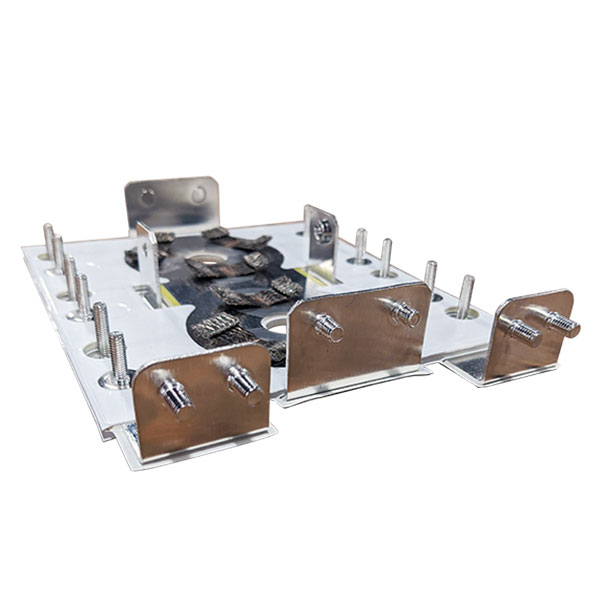